Green Energy
Self-Flushing Debris Filter
The quality of the cooling water intake and the amount of debris in that water affects the operation and performance of the condenser and therefore the thermal performance of the typical steam plant.
Material such as slime, calcium carbonate, calcium sulfate, magnesium dioxide, silt, petroleum products, corrosion products, and the like adhere to the inside of the heat exchanger and condenser tubes. The accumulation and growth of such deposits reduce the overall heat transfer coefficient and will have an adverse effect on the operation of process equipment, plant availability, production, and maintenance cost.
Traditionally, plant maintenance teams isolate and open each heat exchanger or condenser unit periodically in order to clean the tubes manually using high-pressure water jets or mechanical scrapers. This process is labor-intensive, costly, and may require process shutdown. Furthermore, when the equipment returns back to operation, the fouling process begins anew.
there is an online method to clean the heat exchanger or condenser , it is DEBRIS FILTER
Self-Flushing Debris Filter
The debris filter is the ultimate protection for condenser tubes, it is designed to automatically separate and remove fibrous and coarse debris from the cooling water during operation of the cooling system. In order to protect the condenser not only from unwanted particles flushed into the cooling system by the cooling water, but also from particles originating from the cooling water intake channel or pipes themselves, the debris filter should be located as close as practical to the CONDENSER INLET .
Since the debris filter is the last protection in-line of the screening systems in front of the condenser, particular care has been taken to ensure high reliability, availability and performance as well as low maintenance.
Intake screens are often ineffective in protecting heat exchanger tubes from debris. Many plants designed with through-flow traveling screens located upstream of the condenser still experience heavy debris carryover or are victims of macro fouling via mollusk or crustacean growth within the intake tunnel, which causes many clogged condenser tubes. The normal practice is to clean the tubes manually, but this requires an outage or a period at reduced load, depending on the condenser design.
A debris filter or automatic pipe strainers provide the best filtration, ranging from 50 microns to 10 mm. These strainers can be sized to remove the carryover and fine debris that pass through intake screens to prevent buildup inside the condenser or exchanger tubes.
The debris filter replaces a section of the cooling water piping. Water and debris enter into the filter housing, and filtered water exits the screen mesh. Debris larger than the mesh size is trapped over the screen area. Based on the desired setpoint for the increased pressure drop above the clean screen, or on a preset time interval, the debris-cleaning rotor travels over the screen mesh to lift and remove debris from the screen surface. The debris-cleaning cycle lasts only a few minutes. The debris is then discharged into the sewer or into the cooling water discharge from the plant using a small quantity of water.
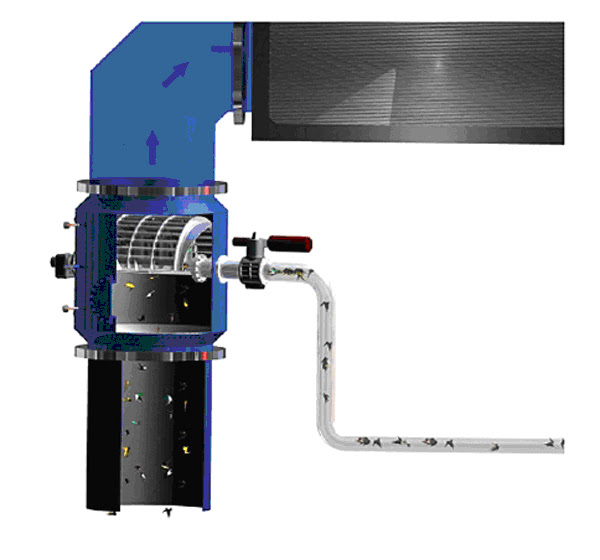
Fixed, semi-spherical shaped filter elements separate the filter area into several independent filter chambers, and consequently no debris can bypass the filter elements. A hood-shaped backwash rotor, located at the raw water side, always covers one filter chamber completely, while a special engineered gear box actuates and rotates the backwash rotor from the clean water side of the filter. The backwash process is automatically initiated by a pressure differential measuring system which monitors debris accumulation permanently.
Not only can the backwash process be triggered automatically by the pressure differential measuring system, the backwash sequence can also be started manually from the local control cabinet.
This is the typical TECHNOS Self-Flushing Debris Filter , and its components shown in the figure above , this system is installed at Most of Thermal Power Station , for its ultimate benefits and advantages .
The attached files are (*.pdf ) files which describe in detail the debris filter , and TECHNOS Catalog
TECHNOS_DEBRIS
DEBRIS_EXPLAIN
-
Dry Gas Cleaning
Exclusive Dry Gas Cleaning Solution to Enhances Gasification Producer Gas (Syngas)Traditionally gasificaton utilizes a Wet Gas Cleaning process to scrub the producer gas of particulates. Wet Gas Cleaning can require a large quantity of water and can contaminate...
-
Solar Heaters For Swimming Pools
Whether fixed or portable, swimming pools can be found in the gardens of many houses throughout the world. Most people begin using their pool in the spring or beginning of summer. Although the air temperature may be pleasant enough, the temperature of...
-
Condenser – Air Extraction Equipment ( 1 Of 3 )
CONDENSER – AIR EXTRACTION EQUIPMENT - Turbines are designed for a particular operating conditions like steam inlet pressure, steam inlet temperature and turbine exhaust pressure/ exhaust vacuum, which affects the performance of the turbines in a...
-
Condensate Polishers At Power Plant
Condensate Polishers at Power Plant“This article is talking about the functions of Condensate Polishers at Power Plants , and Their Types according to their Functionality , .. “ Condensate polishers add operating reliability and flexibility-Condensate...
-
Steam Turbine & Generator Arrangement
STEAM TURBINE ARRANGEMENT The live steam enters the HP turbine through the main stop valves (MSV) and the main control valves (GOVERNORS). After expansion in the HP turbine, the steam is let to the cold reheat line via power assisted check valve. The...
Green Energy